Wir sagen Ihnen, ob Ihr Werkstoff hält, was er verspricht! Bei der Werkstoffprüfung nehmen wir Ihre fertigen Bauteile oder Werkstoffproben genau unter die Lupe.
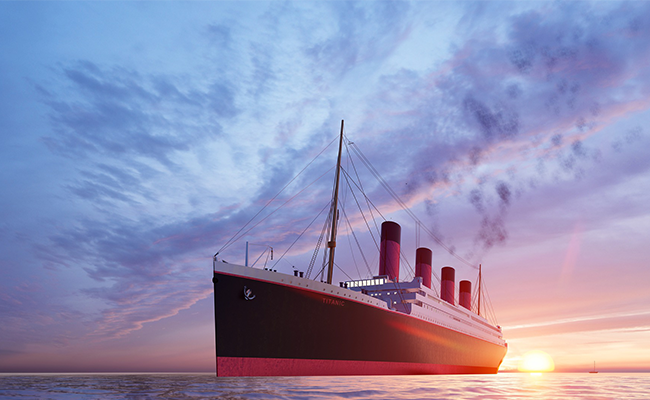
Der Untergang der Titanic lässt auch nach 110 Jahren niemanden kalt. In der Nacht zum 15. April 1912 nahm die Tragödie ihren Lauf. Dass ein Eisberg als Ursache für das Unglück gilt, weiß jedes Kind – doch beim genaueren Hinsehen zeigen sich weitere Gründe.
Der Himmel war kristallklar, das Wasser eiskalt. Sehr niedrige Temperaturen ändern das Verhalten bestimmter Stahlsorten schlagartig. Die Zähigkeit des Konstruktionswerkstoffs nimmt ab, der Stahl wird spröder und lässt sich schlechter verformen. Dieses Werkstoffverhalten hatte einen Anteil am wohl bekanntesten Schiffsunglück der Geschichte: dem Untergang der Titanic.
Die „unsinkbare“ Titanic
Als die Titanic 1912 vom Stapel lief, war sie das größte Passagierschiff der Welt. Das Schiff war 269 Meter lang, 28 Meter breit und etwa 53 Meter hoch. Mit bis zu 60.000 PS erreichte sie eine Geschwindigkeit von rund 39 Kilometer pro Stunde. Die Sicherheitsausstattung galt als Wunder der Technik. Automatisch schließende Wasserschutztüren zwischen 16 wasserdicht abschottbaren Abteilungen vermittelten den Eindruck, die Titanic sei unsinkbar.
Ebenso eindrucksvoll wie die Maße war die Einrichtung. Die Titanic verfügte über eines der größten elektrischen Netze aller Schiffe der Zeit und eine Telefonanlage mit 50 Leitungen. Die Küche verfügte über die zu dieser Zeit weltgrößten Kochstellen. Viele Küchengeräte wurden mit elektrischer Energie angetrieben, etwa Bratöfen und Tellerwärmer. Dank der enormen Schiffsgröße gab es zudem viel Raum für extravaganten Luxus. Die Suiten und Kabinen beinhalteten eine Vielzahl fein geschnitzter Verkleidungen und Furniere aus exotischen Hölzern. Weitere Highlights waren die vielfältigen Turnhallen und das beheizte Schwimmbad.
Werkstoffqualität beeinflusste den tragischen Untergang
Doch aller Luxus konnte den Untergang nicht verhindern. Bis heute ist das Unglück nicht restlos aufgeklärt. Wenig Zweifel gibt es jedoch zum Werkstoffverhalten nach dem Zusammenstoß von Eisberg und Schiff. Bereits 1997 zeigten Materialerprobungen an der Universität Missouri, dass der 1912 verwendete Stahl bei niedrigen Meerwassertemperaturen anfällig für Sprödbruch war. Der hohe Anteil von Schwefel, Sauerstoff und Phosphor sowie eine grobe Kristallstruktur hat die Qualität des Stahls negativ beeinflusst.
Eine ebenfalls geringe Werkstoffqualität hatten die Nieten, die für Bug und Heck der Titanic verwendet wurden. 2012 fanden die Forscher Jennifer Hooper McCarty und Timothy Foecke heraus, dass der Stahl von kleinen Schlackenbrocken durchsetzt war. Entsprechend brüchig waren die Nieten. Ursache ist den Experten zufolge die gleichzeitige Produktion von gleich drei großen Luxusdampfern in derselben Werft: parallel zur Titanic wurden auch die Olympic und die Britannic gebaut. Das Unglück des 15. April 1912 liegt daher auch an der geringen Werkstoffqualität als Folge von hohem Zeitdruck und Lieferengpässen.
Ozeanriesen als Massenprodukt
Aber der Untergang der Titanic führte nicht automatisch zur Verbesserung der Werkstoffqualität. Kurze Bauzeit, geringe Kosten, einfache Konstruktion und große Laderäume hatten bei der Produktion auch nach dem Unglück eine hohe Priorität. So wurden beim Bau der Liberty-Schiffe von 1941 bis 1945 Werkstoffe und Verarbeitungsmethoden eingesetzt, die im eiskalten Wasser des Nordatlantiks für eine Versprödung des Materials sorgten. Risse konnten sich daher leicht bilden und ausbreiten – Ursache war die noch nicht ausgereifte und damals erstmalig im Schiffsbau eingesetzte Schweißtechnik, mit der die Werkstoffeigenschaften zusätzlich geschwächt wurden. Darüber hinaus wurden Schiffe zu dieser Zeit normalerweise noch genietet – so dass der Einfluss des Schweißens in dieser Verwendung noch nicht ausreichend erprobt war.
Die Folgen blieben nicht aus: Mehr als 100 Schiffe sanken aufgrund der mangelhaften Verarbeitungsqualität und dem Unwissen über dieses Materialverhalten. Stets führten die tiefen Wassertemperaturen zu Sprödbruch – der verwendete Stahl war nicht ausreichend kaltzäh. Bestimmte Stahlsorten verlieren ab einer bestimmten Temperaturschwelle abrupt ihre Duktilität – also die Eigenschaft sich plastisch zu verformen, bevor es zum Bruch kommt. Die unterschiedlichen Eigenschaften bei niedrigen Temperaturen hängen von verschiedenen Faktoren ab, etwa der chemischen Zusammensetzung, der kristallinen Struktur, der Korngröße, der Neigung zur Aufnahme von Verunreinigungen, Wärmebehandlungen, der Aufnahme von Schlacke und Prozessen wie Schmelzen, Schweißen, Zerspanen oder Verformen.
Stahl im heutigen Schiffbau
Dank der Materialforschung und -entwicklung gibt es mittlerweile kaltzähe Stähle, die speziell für niedrige Temperaturen geeignet sind. Das starke Absinken der Kerbschlagzähigkeit wird bei den kaltzähen Stählen mit bestimmten Legierungselementen weiter in tiefere Temperaturbereiche verschoben und mit weiteren Nach- und Wärmebehandlungen feinjustiert. Je nach Anwendung müssen die Metalle Temperaturen zwischen 0 und -273 Grad Celsius standhalten. Das hat Auswirkungen auf den Schiffbau.
Stahl ist heute ein zentrales Material für Neubau, Reparaturen und Umbauten von Passagier- und Handelsschiffen oder Yachten. Dabei wird der Schiffbaustahl wechselhaften Belastungen ausgesetzt. Vor allem die Temperaturschwankungen sind ein wesentlicher Faktor. Vor diesem Hintergrund ist Schiffbaustahl gut schweißbar, weist hohe Dehnungswerte aus und ist unempfindlich gegen Sprödbruch.
Mit Prüfungen wird die Kaltzähigkeit von Stählen ermittelt. Bei nahezu allen ferritisch-perlitischen Stählen zeigt sich bei Temperaturabsenkung im Kerbschlagbiegeversuch ein Übergang vom Verformungsbruch zum Sprödbruch. Dieser Steilabfall bedeutet, dass ein Übergang vom zähen zum spröden Bruchverhalten stattfindet. Werkstoffe mit einem derart beschriebenen Übergang sind also bei tiefen Temperaturen sprödbrechend. Sie erfüllen nicht das Kriterium „kaltzäh“ und können daher nicht im Schiffbau verwendet werden. Nur ein Beispiel, wie Werkstoffprüfungen die Sicherheit signifikant erhöhen.